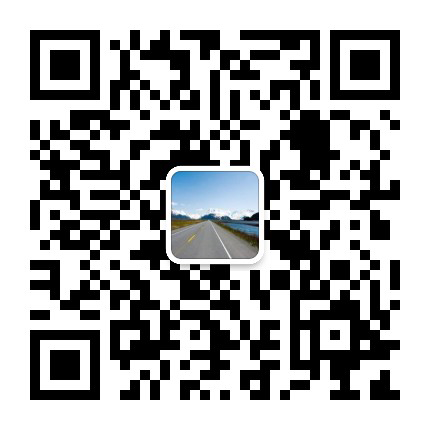
在追求更高体积能量密度的电池制造领域,电池厂商们正以前所未有的热情投身于电芯设计与制造
工艺、以及PACK结构设计的优化之中。其中,叠片工艺凭借其独特的优势,逐渐从边缘走向主流
,成为众多企业在生产高性能电池时的首选。
一、叠片:与卷绕分庭抗礼
叠片工艺在方形电池领域声名鹊起可追溯到2019年。
这一技术通过将电极与隔离膜以层叠方式组合,形成紧凑的平面结构,从而实现了对电池内部空间
的高效利用。相较于传统的卷绕工艺,叠片工艺不仅降低了电池的内阻,提升了放电性能,还因其
均匀的内部结构和更高的安全性而备受青睐。
尽管叠片工艺在生产初期面临着生产效率低、成本较高等挑战,但随着技术的不断进步和智能化检
测设备的引入,这些问题已得到显著改善。如今,多家电池企业已成功将叠片工艺应用于短刀电池
、快充电池及大容量储能电池的生产中,实现了生产效率与产品品质的双重飞跃。
卷绕和叠片工艺各自有其专业领域,过去并没有直接竞争,但情况自2019年发生变化。叠片在方
形电池领域的用户骤然扩量,与卷绕分庭抗礼。
在国内方形电池领域,比亚迪无疑占据了举足轻重的地位,特别是在2020年重磅推出的刀片电池
采用的即是大电芯高速叠片工艺。蜂巢能源同样倡导动力电池“从'卷时代'迈入'叠时代'”,逐渐
明晰“短刀+叠片”的技术标签。
生产效率外,值得注意的是,提升生产良率也是动力电池降低成本的有效手段之一。多家电池称
,其高速叠片工艺解决了行业隔膜褶皱、对齐度不良等缺陷控制与监测痛点问题,生产良品率可
达95%以上,叠片对齐公差在±0.3mm以内。
超级快充电池SFC480采用了高精度叠片技术,叠片精度达到±0.1mm,达到行业先进的水平,叠
片中CCD在线检测,保障叠片精度,叠片后100% CT检测,0不良流出。
CT: 打开叠片电芯的黑盒电芯封装后,内部状况成谜,每一步操作都可能潜藏风险,从细微瑕疵
到严重隐患不一而足。
如堆叠过程中的定位偏差,易致极片偏移,损害对齐精度;极片间的直接接触可能引发翻折、褶
皱;极耳焊接质量不佳则直接导致电池失效;壳体焊接缺陷可能引发漏液,威胁电池安全。此外
,金属异物混入、极片损伤、电解液缺失等问题亦不容忽视。
针对这些潜在问题,即时检测至关重要。然而,电芯内部结构的复杂性使得全面检测变得困难,
拆解检测虽可行但效率低下且存在漏检风险。随着技术进步,现有检测方案已趋于成熟,但叠片
电池因其独特结构,需采用专属检测方法。
对齐度的测试是重中之重。卷绕电池线边一般使用 X 射线检测卷芯边缘位置。但是叠片电池由于
结构不同,暂无法使用 X 射线观测其对齐度,主要使用 CT 检测。
通过采用CT(计算机断层扫描)检测,可以对电池情况进行非破坏性检测,在化成前后测试并比
较,确保用量充足又不会浪费。由于叠片电池堆叠密度更大,极片厚度更薄,对内部金属异物尺寸的控制更为严格。高精度的无损CT可以发现更小的金属颗粒。目前电池制造商通常配备多台CT设备来提高检测效率。
可以看到,工业 CT 在叠片电池的生产过程中发挥出更大作用。像江津蔡司的工业 CT 方案,CT 测试
可以帮助客户完成多种缺陷的甄别,无论在线边抽检还是失效分析,将成品电芯的安全性提高到
新的高度,也区别了各家电芯的质量,让越来越多的电池厂开始意识到 CT 的重要性。
随着技术进步,CT 打开了电芯的黑盒,给出更多种内部缺陷的检测方案,包括对齐度、极片褶皱
、极片间隔、极片破损、极片压伤、极耳翻折、极耳焊接缺陷、电解液不足、金属异物、壳体凹
坑、壳体焊接缺陷、极柱测量等等。
于此同时,对 CT 的要求也在提高。射线管需要有足够的穿透电压,足够的功率。功率越大,扫
描时拍摄的曝光时间越短,可以加快扫描速率。更重要的是,射线源需要有稳定的设计,可以在
大功率条件下依然可以保持超长连续工作时间,即使布置在线边的 CT 也需要7x24 小时使用。并
且始终保持可追溯的测量精度,保证测量的准确性。
蔡司的 METROTOM 系列即使在苛刻的测试需求下,完美的完成了客户要求,可以稳定检出在此
之前的所有工序缺陷,成为业内主要的 CT方案提供者。
在此之上,蔡司更是创造性地把三坐标空间补偿技术应用到计量型工业 CT 领域,2005 制造出全
球首台计量型 CT METROTOM,并不断升级。在保证扫描范围等 CT 性能参数的前提下,又进一
步极大地提高了扫描精度,为计量型工业 CT 提供了可能性以及更加先进的机械结构。